Guide to AS/NZS ISO 9001 for Quality Management System Requirements: Key Guidelines and Benefits
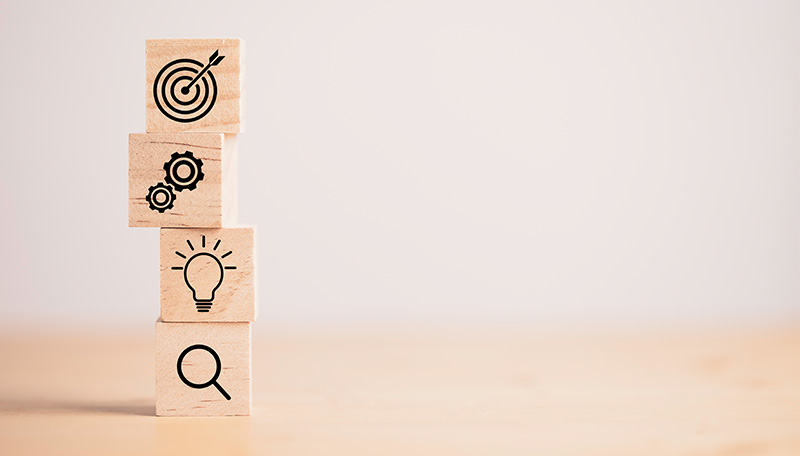
Maintaining consistent quality is important across any industry and stakeholder, whether you are a customer or a business owner.
Achieving quality while meeting regulatory requirements calls for a considerate and documented process via a quality management system. AS/NZS ISO 9001:2016, Quality management systems — Requirements, guides businesses, regardless of its size and process purpose.
Why Have a Quality Management System?
A quality management system (QMS) is the foundation for an organisation’s documented guidelines and procedures. It is a multi-functional tool for ensuring that the operational processes required for providing the product or service are in place, auditing to determine whether these processes are being followed, risk management, and it helps improve leadership, customer experience, employee engagement and overall organisational efficiency.
Consistently satisfy consumer demands for quality
A quality management system helps the organisation to satisfy consumer demands for quality and, in turn, boosts their trust and confidence, leading to long-term customer relationships and increased profits.
Without a quality management system, there’s room for error that impacts not only the quality of a product or service, but it may also impact the customer and their perception of an organisation.
Facilitate continuous process improvement
Improvement is one of seven guiding principles in AS/NZS ISO 9000. Not only is improvement a guiding principle, but AS/NZS ISO 9001 specifies that it should be a permanent objective so that an organisation can see better customer and employee engagement, more robust performance, and better leadership.
Improvement can look like correcting errors, having breakthrough change, innovation or even re-structuring.
Having guidance on improvement is necessary for organisations that need to meet regulatory requirements while addressing future customer and staff expectations.
Comply with statutory and regulatory requirements
Statutory requirements relate to any legislative act, and regulatory requirements relate to any state, national or international laws. Failing to comply with requirements can lead to unnecessary risk and impact on an organisation and its customers.
A quality management system can help meet requirements as it provides a framework for identifying requirements and keeping up to date on any statutory and regulatory changes. Once requirements are identified, an organisation can embed them into their QMS.
Easily identify business risks and opportunities
Organisations may face external or internal risks or both. External relates to the environment in which an organisation operates, from regulatory laws to cultural or financial risks. Internal risks can be resource deficiency or structural risks.
AS/NZS 9001 incorporates risk-based thinking, enabling an organisation to determine any risk that may cause its processes to deviate or produce unwanted results. Risk-based thinking enables organisations to put in preventive measures while also allowing for maximum use of any business opportunities that may occur.
Make decisions informed by evidence and data
To minimise risk, while ensuring continual improvement, an organisation needs evidence-based decision making rather than going off a gut feeling or a guess. A quality management system empowers organisations to make evidence-based decisions through data capture and analysis.
There are many ways to capture data, but each business is different, and each should be able to prove (with data) that it has an effective QMS.
Data capturing is possible through internal or external audits, customer feedback surveys, employee surveys and more. Analysis of the data informs areas for improvement, determines causes of any issues or risks, helps guide whether you are meeting established objectives and provides guidance on what actions are needed.
Maximise value and minimise costs
An effective quality management system can lower costs associated with errors or resourcing and maximise cost through customer satisfaction.
A quality management system can prevent costly mistakes while reducing the time it takes to action corrective measures. Over time, as products or services become consistent and improve, customer satisfaction will increase, leading to opportunities for more profits.
What Role Does ISO 9001 Play?
AS/NZS ISO 9001:2016, Quality management systems — Requirements, provides a comprehensive framework for any organisation, covering off the above core principles of quality management systems.
How QMS standards help organisations
Standards are guiding documents that specify minimum requirements to ensure a product or service is fit for purpose. In this context, quality management system standards provide users confidence and guidance that their processes will achieve their objectives.
Relationship with other quality management standards
While ISO 9001 is the most well-known quality management system standard on the market, it belongs to a ‘family’ of standards, called the ISO 9000 series. For example:
- AS/NZS ISO 9000: 2016, Quality management systems — Fundamentals and vocabulary
- SA TS ISO 9002:2017, Quality management systems — Guidelines for the application of ISO 9001:2015
- AS/NZS ISO 9004:2018, Quality management — Quality of an organization — Guidance to achieve sustained success
Each standard within the series complements one another, building upon information in more specific areas.
Key Requirements of a QMS
It’s important to know why you need a QMS, but it is also important to know the requirements of a quality management system.
Organisational context
An organisation must consider the context in which it operates and determine internal or external issues that could affect the intended results of a QMS. Organisations can achieve understanding by considering legal, competitive, cultural, or economic environments, cultural knowledge, the performance of the organisation, and more.
Involving organisational leadership
Quality management systems include the requirement that leaders must be customer-focused. Leaders must develop and maintain quality management policies that guide the organisation and determine who has authority and decision-making powers within the QMS. It’s vital that leadership takes accountability of the effectiveness of the QMS.
Planning
A requirement of a quality management system is to ensure that it can meet its intended results. Therefore, an organisation needs to include the individuals relevant to the QMS and what is required of them in its plan. It also needs to take into consideration the context of its organisation.
Evaluating performance
Integral to evaluating performance is determining what needs to be measured and monitored and how and when. With the measurement and monitoring results, the organisation can use the data to evaluate the performance and effectiveness of the QMS. The evaluation must be documented and maintained.
Continual improvement
It is a requirement that an organisation identifies and actions opportunities for improvement to meet customer needs and satisfaction. Improvement can range from innovation to improving the effectiveness of the QMS.
Assessing QMS using the Plan-Do-Check-Act cycle
The Plan-Do-Check-Act (PDCA) cycle allows for continual improvement, guiding organisations to:
- Plan: understand organisational context and define the scope of the QMS and its processes
- Do: implement the plan
- Check: monitor and measure processes, products and services, and report the results
- Act: take actions where necessary to improve.
Purchase AS/NZS ISO 9001:2016
AS/NZS ISO 9001:2016 is available for preview and purchase here.
media enquiries
For media enquires, please contact:
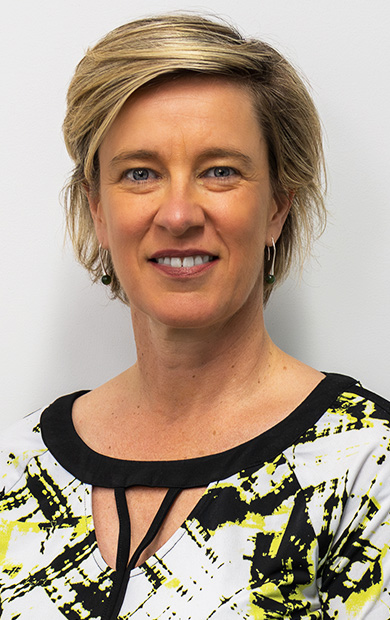